Touching Virtual Reality
Anyone who has ever experienced a Virtual Reality (VR) environment has dreamed of being able to touch the virtual objects and manipulate them with his or her bare hands. Sadly, that requires much more than just a fast graphic board and an immersive visual display. For multi-finger interaction, this requires some kind of wearable force-feedback device, a so-called ‘haptic glove’. The recent growth of the Virtual Reality market resulted in an intensification of development efforts in this technology. These days many teams and start-ups around the world are announcing imminent releases of commercial haptic gloves. Indeed, in the last year there has been one new product announcement almost every month. It is clear that not all new ideas will actually make it to the market, and that not all haptic gloves are addressing the same range of applications. In this paper, the main technical constraints which are faced when designing a haptic glove are addressed with a special focus of the actuation technology. Then, a review of existing devices, past and present projects, comparing their characteristics and performance is provided. Lastly, insights on future developments are sketched.

Introduction
Of all VR interaction devices, the haptic glove is at the same time the most desperately asked for and the most complex to develop. Indeed, each human being not only has a unique hand size and shape but also a pair of hands which are not identical and not even symmetric. In addition, the hand is one of the most sensible parts of the body. It is able to perceive fine details at very large frequencies, but may also develop and perceive large forces. As a consequence, in order to be effective, a haptic glove has to be adaptable to its user. It needs to be lightweight and compact, yet deliver large amounts of power with very low latency.
User requirements and constraints
The sense of touch is extremely complex, and cannot be addressed by a unique actuation principle. For this reason it is common to distinguish between “tactile” and “kinesthetic” touch. Tactile feedback devices provide input to the user’s skin. They try to recreate the sensation of a shape, a texture or in some situations even of thermal properties of a virtual object. Kinesthetic feedback devices apply forces to the skeleton of the user. They create an impression of movement and/or resistance through the muscles. In real life, both feedback types are present when touching an object. In order to experience tactile feedback only, one may try to touch an object placed on a slippery surface, so that it offers no resistance. Similarly, one could isolate kinesthetic perception by touching an object while wearing very thick gloves effectively filtering out the tactile component.
The main user requirements for a haptic glove are as follows: the glove should provide both tactile and kinesthetic feedback, it should be wearable (i.e. not heavy) and should not impede the natural movement of the fingers. Because the need to produce in large numbers to reach an acceptable market price, gloves either need to fit an arbitrary size and form of the hand or should be easily adaptable. Latter constraint is usually addressed by offering a selection of sizes within a certain working range. This approach is to some extent similar when purchasing rubber gloves for the household. However, it is not as simple as that as it becomes tedious when actuators need to be placed very precisely relative to the user’s anatomy.
Haptic gloves in Simulation
Simulation is nothing but an imitation of the real situation or process. By simulation, one can simulate the real like situation and get the exact idea of correction in the process or a product. In today’s R&D based market, simulation is an essential part for some industries. Simulation reduces the cost of trial and error and hence, ultimately becomes a deciding factor in the overall price of the product in the market.
Today, designers and engineers can’t interact with a product until they build a physical prototype. With Haptic Gloves, it is possible for teams to touch and interact with 3D models throughout the product design process.
Recently, UK firm FundamentalVR is enhancing its VR surgery simulation platform with the addition of the HaptX Glove, giving surgeons haptic feedback directly to their hands. Surgical Haptic Intelligence Engine of FundamentalVR is designed to mimic the feel of operating on various types of human tissue, from subcutaneous fat to muscle and bone too. The platform, which has recently won an innovation award at the SXSW festival in Austin, Texas, is hardware agnostic and it can also be used with a range of off-the-shelf haptic equipment. Until now, this has consisted basically of haptic pens and arms that simulate the surgical tools. But with the integration of the HaptX Glove, users will now be able to engage directly with the VR simulation via their hands, guiding a tool held separately or manipulating the patient’s body.
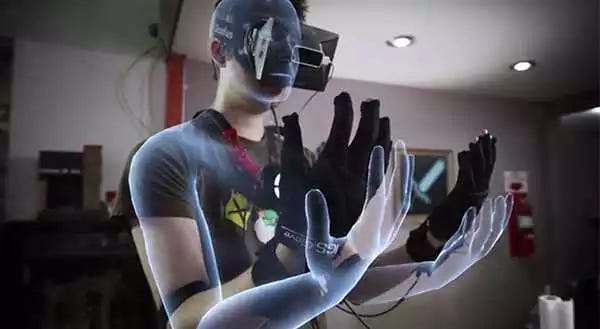
Haptic gloves in training
Training is a crucial part of any industry. Training employees with traditional methods seem boring nowadays. Training can be made live and interactive with the use of VR. VR helps for creating a real like imaginary environment and a new employee can witness the exact conditions he/she will be looking after in nearer future.
Haptic gloves can better training experience. Fire safety, locomotive training, nuclear reactor operator training, etc. are the fields where the haptic gloves may prove its expertise.
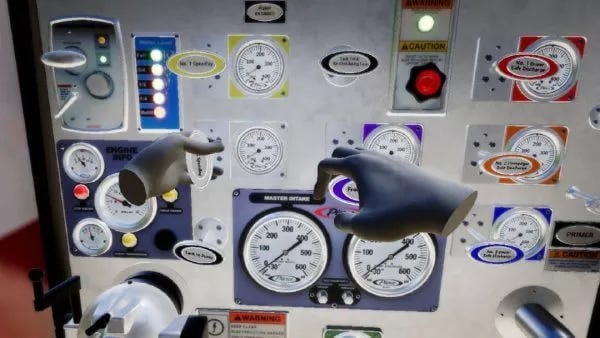
Conclusion
The haptic gloves come up with the rejuvenating wave for many industries. They help in various processes like simulation, training as well as designing as we have seen. It reduces a large amount of time and cost for the manufacturer is well. Till date, there are many technological changes that are happening in this particular field. But still, the current versions are much better and we hope that we get the best out of it in the near future.
An Article By: C&L Team
DISCLAIMER
Shaastra TechShots' publications contain information, opinions and data that Shaastra TechShots considers to be accurate based on the date of their creation and verified sources available at that time. It does not constitute either a personalised opinion or a general opinion of Shaastra or IIT Madras. The information provided comes from the best sources, however, Shaastra TechShots cannot be held responsible for any errors or omissions that may emerge.